FlatFish - Autonomous inspections in the deep sea
The underwater inspection of offshore industrial plants is a complex, expensive and risky undertaking. Clumsy, cable-bound submersible vehicles, so-called Remotely Operated Vehicles (ROVs), and specialized divers have so far carried out maintenance work in the sea in daring maneuvers - accompanied and supported by one or more maintenance vessels. An operation at sea costs between 100,000 and 300,000 euros per day. DFKI is currently developing an autonomous robot that could significantly simplify the underwater inspection of offshore facilities in the future.
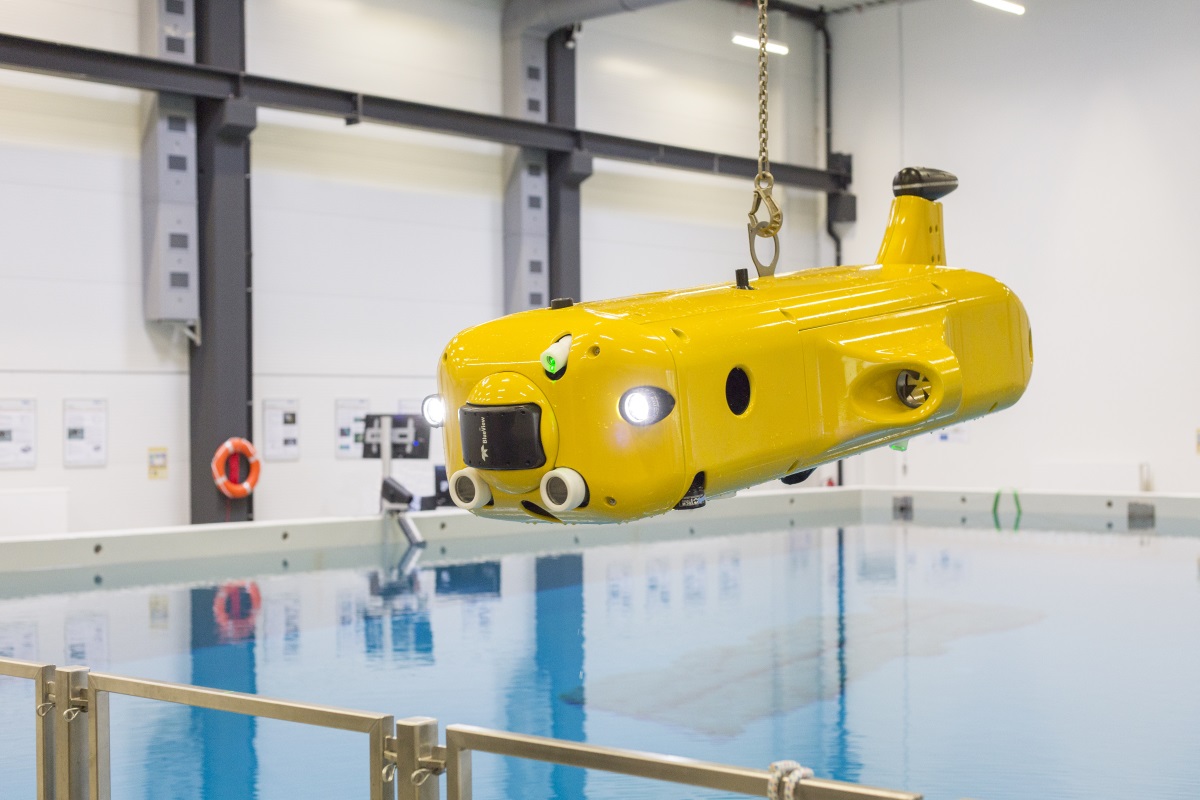
It is pitch dark and freezing cold, the water pressure is enormous. In the depths of the sea there are hostile conditions. Two spotlights suddenly appear from a distance. A small, yellow submarine emerges from the darkness. Its name: FlatFish. Its destination: a faulty undersea cable. Its mission: An autonomous underwater repair in the deep sea. The special feature of this underwater vehicle: No human being is on board - or even close to it. The diving robot works completely autonomously in the ocean. Until now, humans have had to laboriously operate inspection submarines from a ship via water cables and supply them with power. FlatFish, on the other hand, will carry out underwater missions independently and wirelessly in the future - if its developers have their way.
Power supply and data exchange under water
FlatFish was developed by the German Research Center for Artificial Intelligence (DFKI) in cooperation with the Brazilian Institute of Robotics (BIR) and Shell. The vehicle is designed for a longer stay on the seafloor.
Via a docking station located on the seabed, the mini-submarine automatically uploads and downloads data and draws its power from there. FlatFish can stay and operate at a maximum distance of ten kilometers from the docking station. Using acoustic or visual sensors, FlatFish records data from various targets. Technicians on land define the task and send instructions to the docking station. FlatFish leaves and after a successful mission returns to its "garage" on the seabed where it awaits new orders. The vehicle is specialized in detecting damage to underwater cables, pipelines or moorings of oil rigs and wind turbines.
Autonomously on the move with the help of AI algorithms
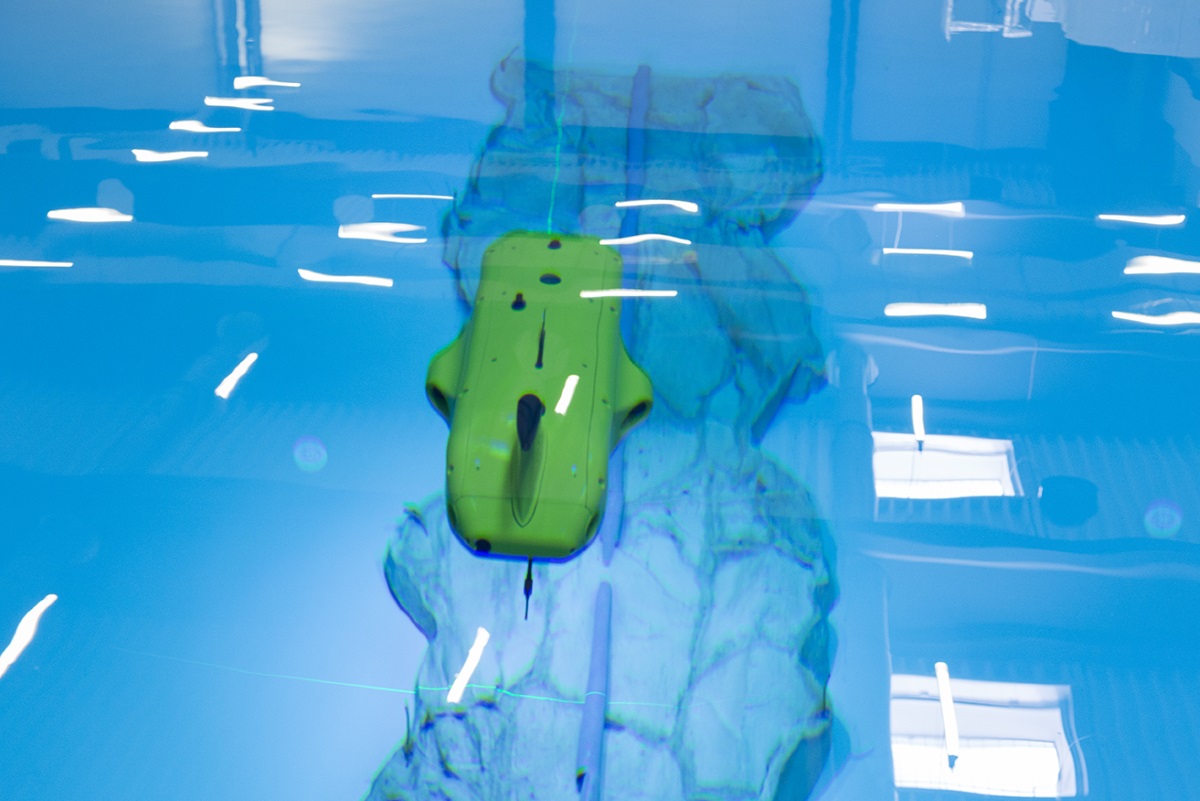
The programmers of FlatFish used AI algorithms for the first time in the field of navigation: The underwater vehicle builds up the maps of its surroundings on its own, locates itself within space and navigates to its destination according to its mission. By means of a sophisticated sensor system and the associated algorithms, FlatFish also recognizes any obstacles it can avoid autonomously and finds its way back to the planned route on its own. This also means that monitoring is fully automated. As a result, the operators receive a three-dimensional and high-resolution presentation of the detected underwater object - for example a gas or oil pipeline. Cracks, deformations or overgrowths can be detected and recorded.
The advantages of the system compared to the previous practice of underwater missions: Flatfish travels faster than a cable-bound submersible vehicle, does not require expensive accompanying maintenance vessels, can be deployed flexibly and at short notice without charter preparation and independently collects inspection data - all this at a sea depth of up to 300 meters.
Maintenance vessels no longer necessary for inspections
This would eliminate one of the central difficulties of offshore maintenance. After all, supplying vehicles with energy has always been one of the greatest challenges for underwater robotics. The more power the devices require, the more dependent they are on external power sources such as ships or underwater cables. All the more significant is the fact that FlatFish can charge its battery autonomously via a docking station on the sea floor.
The project is currently in the pre-commercialisation phase. It is clear, however, that not only industry and economy will benefit from this novel underwater robot, but also science. After all, maritime expeditions at great sea depths are also possible at any time with FlatFish.
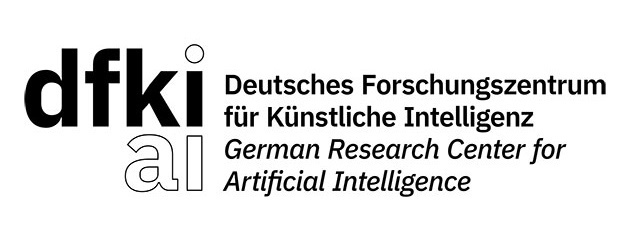
Application facts
Image Recognition and Understanding
Sensors and Communication
- Autonomous Driving and FlyingPredictive AnalyticsIntelligent Assistance SystemsRoboticsIntelligent Sensor Technology
DFKI Standort Bremen
University/Research Institution
Website
Ground Truth Robotics GmbH
Royal Dutch Shell
Brazilian Institute of Robotics (BIR)
Saipem S.p.A.